Risparmio energetico e produzione flessibile con Atlas Copco
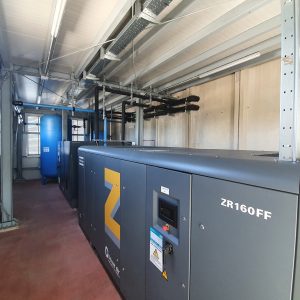
L’acqua oligominerale Santa Maria, che sgorga da una sorgente all’estremità sud-orientale della Sicilia, è imbottigliata con cura e precisione nello stabilimento di Modica che ha recentemente rinnovato il suo impianto di aria compressa.
Il nuovo impianto, basato su tecnologia e progetto Atlas Copco, garantisce la purezza dell’aria e l’ottimizzazione dei consumi energetici grazie all’architettura modulare del sistema di aria compressa, alla tecnologia Oil-free dei compressori ed al programma di gestione e automazione della sala che garantisce in ogni momento un utilizzo efficiente di tutti i macchinari installati.
Lo stabilimento di Siam produce circa un milione di bottiglie al giorno di acqua minerale naturale, frizzante o leggermente frizzante destinate a utilizzi diversi: per l’utente singolo, per la famiglia, per i ristoranti e per le mense. Si tratta di due le linee produttive: una è dedicata esclusivamente a bottiglie di acqua naturale di due litri, mentre l’altra è dedicata ai formati dal mezzo litro ai due litri sia di acqua naturale che di acqua addizionata di anidride carbonica. La richiesta di aria compressa per la realizzazione di questi prodotti varia da un minimo di 300 m3/h a un massimo di 2.000 m3/h a pressione operativa di 29 bar(g).
La sfida di Atlas Copco, di fronte a una così elevata fluttuazione della richiesta, è stata quella di progettare un impianto in grado di adeguare in ogni momento il flusso dell’aria alle effettive necessità del cliente, con conseguente ottimizzazione dei consumi energetici. È stato pertanto implementato per Siam un programma di automazione e gestione realizzato su specifiche di progetto Atlas Copco che legge in ogni momento dagli apparati di misura installati nell’impianto i dati di pressione, di portata dell’aria e di consumo energetico, attivando quindi le macchine più idonee in funzione del flusso d’aria richiesto.
Grazie al sistema ZD Flex di Atlas Copco, in base al quale una serie di serbatoi di bassa pressione disaccoppia le due sezioni di compressione rendendo le singole macchine perfettamente indipendenti fra loro, è stata garantita la flessibilità di esercizio e la possibilità di fornire aria di bassa pressione per i servizi ausiliari dello stabilimento. Nello specifico, sono stati installati due compressori bistadio a vite Oil-free raffreddati ad acqua con essiccatore ad assorbimento integrato, e due booster Oil-free a pistoni orizzontali e contrapposti. Per seguire al meglio le variazioni della produzione, sono stati inoltre previsti un booster con tecnologia VSD (Variable Speed Drive) e il compressore ZR 160 VSD+, insignito del premio “miglior prodotto dell’anno 2019” dalla rivista Plant Engineering. Questo compressore, grazie al suo motore a magneti permanenti in classe energetica IE5 (efficienza del 97%) ed al suo innovativo stadio di compressione, consente di raggiungere una efficienza di circa il 12% maggiore rispetto ai modelli precedenti, assicurando un minor impatto ambientale.
L’architettura modulare del progetto si è dimostrata vincente anche durante il lockdown, verificatosi nel passaggio dal vecchio impianto al nuovo. L’installazione era già infatti prevista in due fasi: la prima fase prevedeva l’inserimento di due dei sei compressori acquistati in una nuova area appositamente costruita per l’ampliamento dell’impianto, mentre durante la seconda fase sarebbero stati sostituiti gli ultimi compressori Atlas Copco con i nuovi modelli. Seguendo quindi questo processo anche durante il lock-down, scattato fra la prima e la seconda fase del progetto e coinciso con un aumento della richiesta di acqua minerale, è stata garantita la continuità di produzione nonostante l’emergenza sanitaria.
“Lavoriamo con Atlas Copco da circa vent’anni, quando abbiamo acquisito i nostri primi due compressori, e siamo sempre rimasti soddisfatti sia per l’affidabilità della tecnologia impiegata che dal grande spirito di collaborazione che abbiamo riscontrato in ogni occasione. Anche per l’installazione ed il collaudo del nuovo impianto siamo stati seguiti con professionalità e siamo stati supportati inoltre nella redazione della dichiarazione DM 329 necessaria per la messa in servizio in sicurezza delle attrezzature in pressione. Aggiungo che la silenziosità dell’impianto e la riduzione di vibrazioni sono state determinanti per migliorare l’ambiente di lavoro nella nostra sala compressori”, afferma Ottavio Dimartino, Responsabile Produzione di Siam.
“I dati per il monitoraggio forniti da Energy Team, la Energy Service Company che ci ha affiancato nel progetto ed ha fornito la strumentazione di misura di portata e di potenza, hanno evidenziato dei consumi specifici delle macchine superiori alle aspettative, con miglioramento complessivo dell’efficienza dell’impianto di circa il 25% che conseguentemente comporta un risparmio economico per il cliente. Ciò è stato merito sicuramente del nostro progetto combinato con una tecnologia innovativa, ma anche del programma di automazione e controllo che gestisce tutto l’impianto e che attiva i diversi compressori per ottimizzare il flusso di aria compressa in maniera costante, inoltre la sala compressori è monitorabile da remoto attraverso i più comuni device (smartphone, tablet, ecc.). Possiamo pertanto dire che le prestazioni della nuova sala compressori ci stanno dando grandi soddisfazioni. Ne siamo molto orgogliosi”, afferma Giorgio Ceron, Project Engineer di Atlas Copco che ha progettato l’impianto e seguito tutto il suo processo di implementazione.
Contenuti correlati
-
L’importanza della contabilizzazione dell’acqua: una risorsa vitale da preservare
La crescente scarsità d’acqua, confermata dai recenti dati dell’Ispra, che segnalano in Italia una diminuzione della disponibilità idrica del 18,4% rispetto alla media storica, evidenzia un’urgenza: l’acqua è una risorsa non più garantita e richiede un controllo...
-
Compound termoplastici, Schneider Electric supporta la decarbonizzazione di Lati
Lati, tra i più importanti produttori di compound termoplastici tecnici, prosegue nel suo percorso di decarbonizzazione con il supporto delle tecnologie Schneider Electric, in particolare la piattaforma per il monitoraggio e gestione dell’energia EcoStruxure Power Monitoring Expert....
-
Quando l’acqua è vita
La piattaforma PcVue è stata scelta per realizzare il sistema di supervisione e gestione dell’acqua della diga di Karian, in Indonesia Situata nella provincia di Banten, a un’ora di auto da Giacarta, la diga di Karian testimonia...
-
EIMA International: Rivulis presenta nuove soluzioni innovative per la microirrigazione
Rivulis parteciperà a EIMA International (Padiglione 22, Stand A15), la prestigiosa fiera biennale delle macchine agricole, in programma a Bologna dal 6 al 10 novembre 2024. La kermesse sarà l’occasione per presentare l’azienda completamente integrata, dopo la fusione...
-
Accadueo, la filiera del settore idrico si incontra a Bari dal 27 al 29 novembre
Le nuove tecnologie per il riuso delle acque reflue; il ruolo della transizione digitale nella gestione dei sistemi idrici; le tecniche più all’avanguardia per la dissalazione; le nuove normative UE per la depurazione; le criticità e le...
-
L’acqua è preziosa e va gestita bene
L’esigenza di ottimizzare la distribuzione dell’acqua in provincia di Caltanissetta ha spinto il gestore del servizio idrico locale a realizzare una moderna infrastruttura di telecontrollo, impiegando Ignition Caltaqua Acque di Caltanissetta è il gestore del servizio idrico...
-
La sostenibilità è al centro degli obiettivi di sviluppo di Schneider Electric
Schneider Electric ha rilasciato i suoi risultati di impatto di sostenibilità per il secondo trimestre del 2024, nel quadro della comunicazione dei suoi risultati finanziari semestrali. Il monitoraggio e la divulgazione dei progressi trimestrali del programma Schneider...
-
Siccità: usare l’AI per ridurre le perdite nella rete idrica
Acqua, un problema dalle antiche radici, soprattutto a sud, soprattutto in questo momento storico in cui la siccità si fa sentire più che mai. “La Regione Sicilia dovrebbe puntare ad assumere un ruolo di primo piano nel...
-
Un occhio all’aria compressa
L’automazione può migliorare efficienza energetica, produttività e flessibilità in azienda. E il monitoraggio dei sistemi di aria compressa? Una soluzione ifm electronic garantisce anche in questo caso risparmi consistenti a fronte di investimenti contenuti Ifm è una...
-
Ridurre il consumo di aria compressa
Obiettivo: individuare le perdite per eliminarle in modo semplice e strutturato. Festo e GMM effettuano un revamping dei sistemi dello storico produttore di cioccolato Venchi, così da aumentare il risparmio energetico e diminuire la CO₂ Con oltre...