Riciclare è meglio
Dalla rivista:
Fieldbus & Networks
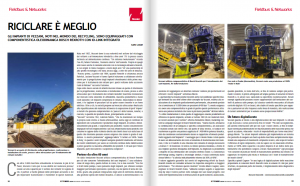
Gli impianti di Vezzani, noti nel mondo del recycling, sono equipaggiati con componentistica oleodinamica Bosch Rexroth con IO-Link integrato
Con oltre 2.000 macchine attualmente in funzione in più di 50 Paesi, Vezzani è nota per la sua abilità nel realizzare presse/ cesoie ad alta capacità per il settore dei rottami; in ragione di ciò, è partner a livello globale delle principali acciaierie e dei più importanti trasformatori e rivenditori di questi materiali. Nata nel 1962, Vezzani deve la sua notorietà nel settore del riciclaggio dei rottami a un’innovazione introdotta a fine anni ’70: la pressa cesoia inclinata ad alimentazione continua. “Un sistema rivoluzionario” ricorda l’ex AD, Mario Pastorino, ‘memoria storica’ dell’azienda. Proprio in quegli anni nasce anche il connubio vincente con la tecnologia idraulica Rexroth, le cui origini in Italia risalgono a metà degli anni ’50: una partnership di alto profilo tecnologico che dura ancora oggi, a oltre 60 anni di distanza. “Ancora prima, a partire dal 1964, quando Rexroth si chiamava ancora Ruhrital, Luciano Vezzani e Hanno Speich iniziarono a collaborare strettamente per la progettazione degli impianti oleodinamici delle prime macchine per il trattamento dei rottami per i parchi rottame delle acciaierie Falck di Milano” racconta Pastorino. Dopo oltre mezzo secolo di attività Vezzani rimane un punto di riferimento per la progettazione, realizzazione e installazione di cesoie, presse e altre attrezzature per il trattamento dei rottami metallici; macchine riconosciute dal mercato come sinonimo di affidabilità, massima produttività e bassi costi operativi. Gli impianti comprimono il rottame, riducendone le dimensioni, e lo tagliano in pezzature tali da poter essere inserite in un forno elettrico. Oltre a ciò, la società propone sul mercato attrezzature finalizzate alla riqualificazione del materiale attraverso la separazione di parti ‘impure’ e metalli che possono compromettere la ‘purezza’ della fusione, nonché, a cascata, la qualità del prodotto finale, principalmente acciaio. “Vezzani” racconta l’AD, Gabriele Merlo, “che ha mantenuto nel tempo la propria sede storica a Ovada (Alessandria), vanta oggi un centinaio di dipendenti ed è attualmente il produttore degli impianti, di settore, dimensionalmente più grandi, e soprattutto più produttivi. Siamo costantemente impegnati nel loro miglioramento e ad essi affianchiamo nuovi prodotti, che creiamo in ragione delle richieste dirette dei clienti stessi e/o sulla base di quelle che riteniamo possano essere esigenze che siamo in grado di soddisfare. La nostra produzione” aggiunge Merlo “è tuttora al 100% ‘made in Italy’, in quanto i nostri impianti vengono prodotti totalmente all’interno dei nostri stabilimenti, per avere un controllo continuo della fabbricazione e poter garantire la massima affidabilità dei prodotti. E ciò vale per l’intero impianto, parti meccaniche e carpenteria comprese”.
Partner da oltre 60 anni
Fin dalla fondazione Vezzani utilizza componentistica di Bosch Rexroth per ciò che concerne l’oleodinamica dei suoi impianti. È una collaborazione di lunga data, quella tuttora in corso, tra le due società: “Sia che si tratti delle pompe, cuore pulsante degli impianti, per ottenere sempre maggiori performance (pressioni e portate), sia dal punto di vista del controllo, grazie alla graduale integrazione negli anni di elettronica dedicata alla gestione spinta del motion idraulico, ci unisce la determinazione e la passione di raggiungere un obiettivo comune: rendere più performanti ed efficienti i nostri impianti” sottolinea Merlo. La partnership ha trovato positivi riscontri anche nel soddisfare specifici bisogni derivanti da una delle ultime sfide concepite da Vezzani, relativa alla realizzazione di un impianto particolarmente performante, che prevede portate che si avvicinano ai 10.000 l/min con pressioni di 400 bar: “La nostra esigenza era avere una componentistica in grado di gestire queste performance attraverso una potenza installata che fosse la più bassa possibile” dichiara Merlo. “La sfida fondamentale è stata quella di raggiungere elevata produttività ed efficienza in questo impianto, arrivato a trattare 180 t/h con materiali misti, un record assoluto per il settore” afferma Beniamino Siboni, marketing content & campaign manager in Bosch Rexroth Italia. “Siamo riusciti, attraverso la combinazione di un’adeguata e specifica componentistica, ad assicurare il risultato voluto dal cliente che, dal punto di vista tecnico, si traduce nel trasformare e gestire una potenza applicata di 1.400 kW in potenza idraulica, dato da considerare sostanzialmente basso se rapportato all’elevata produttività raggiunta dall’impianto”. Il vantaggio per il cliente finale è stato quello di avere un abbassamento del costo a tonnellata di trasformazione del materiale, il che si è tradotto in una riduzione del consumo di energia necessario a trattare 1 t di materiale. In sintesi, la minore potenza installata, a fronte di una migliore gestione dissipativa dell’impianto, ha migliorato la produttività a dispetto di una diminuzione del consumo elettrico totale. La consistenza dell’energy saving, rispetto a tecnologie similari, è stata confermata dallo stesso Merlo e “si attesta indicativamente intorno dal 30% al 40%”. Il valore aggiunto garantito dai servizi di engineering offerti da Bosch Rexroth risiede nel connubio virtuoso tra risparmio energetico e maggiori performance. “Per ottenere questo risultato” ricorda Marco Gagnor, sales engineer in Bosch Rexroth Italia, “abbiamo sempre seguito e supportato step by step il nostro partner nello sviluppo dei suoi nuovi progetti, così come nell’implementazione e ottimizzazione di quelli esistenti, analizzando, quando possibile, lo stato dell’arte, al fine di rendere sempre più performanti i sistemi, in primis attingendo all’ampia gamma di soluzioni di Bosch Rexroth e, in alcuni casi, lavorando su specifiche customizzazioni. Alcuni esempi significativi possono essere rappresentati dall’evoluzione dei controlli di potenza sulle pompe, dal classico controllo meccanico all’attuale controllo digitale HS5 on-board, allo studio di tenute specifiche per sopperire a pulsazioni ad alta frequenza sulla linea di mandata, alla realizzazione di cursori asimmetrici per le valvole servo proporzionali 4Wrle”.
Un futuro digitalizzato
Vezzani guarda al futuro e alla digitalizzazione dei suoi impianti. La strada è già tracciata e serve percorrerla fino in fondo: “Più dati raccoglieremo, più avremo informazioni utili per noi e per i nostri clienti, al fine di individuare eventuali problematiche nel funzionamento delle macchine prima che questi accadano, riducendo i rischi di improduttività per fermo macchina” spiega Merlo. “Su alcuni impianti abbiamo già implementato un sistema che permette di eseguire un check-up della macchina semplicemente impostando una sequenza di movimenti a impianto scarico, allo scopo di testare l’efficienza di ogni componente, così da sapere se sta lavorando effettivamente al 100% delle capacità e da poter disporre di un indice delle problematiche che potrebbero sorgere a breve. Naturalmente” egli prosegue “ciò consente di praticare forme di manutenzione predittiva da remoto e di rapportarci in maniera più mirata e fruttuosa con i team di manutenzione dei nostri clienti”. Specifica quindi Gagnor: “In una logica di digitalizzazione delle macchine proponiamo le soluzioni Bosch Rexroth come le valvole IO-Link per poter sfruttare, da qualsiasi parte del mondo, il miglioramento della diagnostica degli impianti”.
Bosch Rexroth – www.boschrexroth.com/it/it
Contenuti correlati
-
Riciclo automatizzato delle batterie con Bosch Rexroth
Aumenta a livello globale la presenza, e non solo sulle strade, di veicoli elettrici. In quest’ottica un ruolo di primo piano lo gioca sempre di più il riciclaggio delle batterie giunte a fine vita, e ciò in...
-
Sensori e connettività per dare nuova vita alla plastica
Utilizzando i sensori e la tecnologia di ifm, il Gruppo austriaco Erema è in grado di riciclare la plastica con la massima efficienza e con un uso attento delle risorse, gestendo i dati in modo efficace e...
-
Soluzioni di automazione Bosch Rexroth per la produzione di batterie per EV
La domanda di soluzioni per l’accumulo di energia è in questa fase storica più che mai elevata, spinta dall’espandersi delle vendite di auto elettriche, dal proliferare di dispositivi elettronici e dalla diffusione di nuove tecnologie per l’edilizia....
-
Stampe flessografiche senza scarti grazie alle macchine di Expert con tecnologia Bosch Rexroth
Drupa è la vetrina internazionale dove ogni quattro anni il mondo dell’industria della stampa mette in mostra il meglio della sua produzione. Negli undici giorni della kermesse tedesca (28 maggio – 7 giugno) sarà presente Expert, società...
-
Bosch Rexroth e PetrolValves elettrificano le valvole di processo sottomarine
Bosch Rexroth e PetrolValves hanno siglato un Memorandum di Intesa per collaborare all’elettrificazione delle valvole di processo sottomarine con elevati requisiti di Safety Integrity Level, come le Subsea Safety Isolation Valves (SSIV). Entrambe le società stanno già...
-
Bosch Rexroth scommette sull’idrogeno per una mobilità più sostenibile
La sostenibilità è un caposaldo del patrimonio valoriale di Bosch Rexroth, impegnata nello sforzo di consegnare alle generazioni future un mondo in cui possano prosperare. È un intento di grande respiro che l’azienda persegue nella certezza che...
-
Da Bosch Rexroth un portfolio di soluzioni dedicate all’industria dell’idrogeno
Bosch Rexroth sta fornendo, nell’ottica di un possibile raggiungimento della neutralità climatica, un importante contributo alla creazione di un’economia dell’idrogeno. Grazie anche all’esperienza maturata in materia di motori a combustione interna riconvertiti per l’idrogeno, attualmente il portfolio...
-
Agritech, Bosch Rexroth rende più efficienti gli sprayer di Caffini
È lunga un secolo la storia di Caffini, iniziata nel 1924 in forma di piccola officina di paese, trasformatasi poi in concessionaria per la vendita di macchine agricole destinate ai trattamenti antiparassitari, fungicidi e altro. Infine, dal 1978,...
-
Abilitare l’industria sostenibile e 4.0
Digitalizzazione, Internet of Things e interconnessione delle macchine sono le tecnologie che meglio realizzano l’industria sostenibile e 4.0: fra le soluzioni in linea con questo figura lo standard IO-Link Leggi l’articolo
-
Più smart e sostenibili con IO-Link
Macchi si affida a Gefran quale partner di fiducia in virtù di un pacchetto di soluzioni completo volto a potenziare l’efficienza produttiva degli estrusori, tra cui spiccano i sensori di pressione di Melt con uscita digitale IO-Link...