Caro bollette: come gestire meglio gli asset di fabbrica per contenere i consumi?
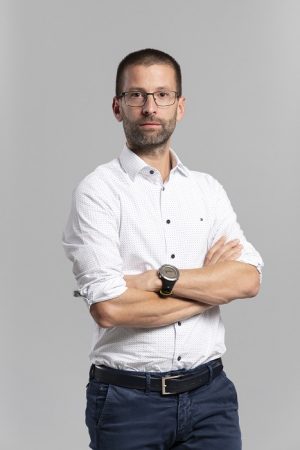
Caro bollette: un tema di forte attualità che riguarda, non solo le famiglie italiane, ma tutte le imprese, ancor più quelle aziende particolarmente energivore. L’impatto dell’aumento di gas ed energia elettrica, dovuto ai rincari delle materie prime, si sta rivelando molto importante per queste organizzazioni che, di fatto, consumano molto per produrre al meglio i propri beni.
Per questo il governo, dopo interventi per mitigare i rincari a fine 2021, sta pensando, proprio in questi giorni, a introdurre nuovi fondi per il 2022, anche sotto la pressione di associazioni di categoria come Confindustria. Già approvata dal Ministero dello Sviluppo Economico, con il Decreto Energia, la possibilità di rateizzare gli importi di energia e gas di maggio e giugno fino a 24 mesi, con la garanzia che potrà essere rilasciata da SACE, fino al 90% degli importi dovuti ai fornitori. Non solo, si muove anche l’Europa: Bruxelles adotta misure per dare flessibilità ai governi nell’aiutare cittadini e imprese.
Secondo le rilevazioni di Arera, le imprese più piccole pagano il 27,8% in più della media dell’area euro con un consumo medio annuo tra i 500 e i 2.000 MWh per un costo di 155,6 euro al MWh; le imprese più grandi hanno con consumi tra i 70.000 e i 150.000 MWh per un impegno di spesa di 95,6 euro al MWh.
Come gestire meglio gli Asset della fabbrica e contenere i consumi e gli sprechi?
È difficile correlare il comportamento dei propri asset al consumo di energia e prevedere il dispendio energetico delle proprie linee di produzione. Infatti, nella maggior parte dei casi le imprese consumano molta energia necessariamente per far funzionare i propri macchinari (come, per esempio, forni ad alte temperature) e, in attesa dei fondi promessi dallo stato (che si stanno varando con leggi ad hoc in questi giorni), le aziende devono attivarsi in un massimo controllo sugli sprechi, eliminando tutto il ‘superfluo’.
Come è possibile monitorare i dati e scoprire perdite e inefficienze del proprio impianto?
Spesso le aziende hanno a disposizione molteplici set di dati che provengono da fonti diverse e rendono difficile un’analisi realistica. Solo con un monitoraggio reale dei dati, pertanto, è possibile avere cognizione di causa delle aree dove è richiesto un maggior dispendio di energia o dove si sta sprecando energia e correre quindi ai ripari con azioni correttive.
Diventa più che mai fondamentale, quindi, il monitoraggio reale dei dati provenienti da fonti diversificate per prevenire gli sprechi e ottimizzare i consumi: l’efficientamento energetico insieme a una produzione più efficiente sono di certo un primo passo che inizia, appunto, dall’analisi dei dati.
Al di là delle decisioni governative, l’azienda manifatturiera può oggi contare sulle giuste tecnologie come sistemi di IIoT Data Management per calcolare e ottimizzare il proprio consumo energetico.
Quale strumento scegliere per monitorare i consumi di fabbrica?
Il centro del sistema di data management è la scelta di affidarsi a strumenti IIoT che aiutano l’industria a governare i dati in modo strutturato ed efficace al fine di raggiungere i propri obiettivi: monitorare i propri consumi significa, in definitiva, ottenere un vantaggio competitivo.
Quali funzionalità supportano l’impresa nel monitorare i consumi?
- offrire una dashboard utente intuitiva con uno spaccato storico e in real time del monitoraggio di alcune variabili delle macchine;
- generare alert e notifiche in caso di variazioni consistenti sulle performance della macchina e sui consumi;
- monitorare l’efficienza della macchina (calcolo indice OEE);
- offrire al management una panoramica dell’andamento e una visibilità generale dell’intero impianto produttivo.
Questo monitoraggio approfondito può offrire informazioni cruciali sulle aree a maggior dispendio energetico e consente quindi di prendere decisioni tempestive e correttive per consentire all’azienda di utilizzare solo il giusto livello di energia, evitando gli sprechi.
Si tratta, infatti, di piattaforme di raccolta dati che si interfacciano con il campo e veicolano le informazioni su tutti gli applicativi aziendali. Grazie a questi sistemi è possibile comunicare con macchine e dispositivi sul campo, anche se dotati di tecnologie differenti tra loro, e uniformare le informazioni generate per offrire un’interfaccia standard che raccoglie dati e informazioni sul funzionamento delle macchine e sul processo produttivo.
In questo modo è, quindi, possibile intervenire con decisioni informate e più mirate sulle macchine per rendere la produzione quanto più eccellente possibile.
Attraverso il monitoraggio degli asset aziendali (le linee di produzione), l’azienda può così avere un quadro completo sui propri consumi energetici (anche in tempo reale), può effettuare le analisi sui dati in modo intuitivo e dinamico, generando un’ottimizzazione complessiva nell’utilizzo dei propri impianti, prestando così un occhio al risparmio diretto in termini economici ma anche al benessere del nostro ambiente.
di Michele Lafranconi, Head of Sales - Software Products
Contenuti correlati
-
Dolomiti Energia supportata da Impresoft per fare innovazione in sicurezza
La cybersecurity è diventata una priorità per le aziende, da quando la tecnologia e l’innovazione hanno permeato i processi di produzione e di comunicazione. Da questa consapevolezza è nata la necessità del Gruppo Dolomiti Energia, a seguito...
-
Tagliare i costi dell’energia e le emissioni si può con Energy Manager di Emerson
Emerson ha lanciato la sua nuova soluzione Energy Manager, un’offerta di hardware e software pre-ingegnerizzati progettata per semplificare il monitoraggio dell’elettricità in ambito industriale con una configurazione rapida e un funzionamento intuitivo. La soluzione Energy Manager viene...
-
Agricoltura e bilanciamento reti: il Bess come risorsa
Con l’aumento dei costi delle materie prime e dell’energia anche il comparto agricolo sta vivendo un momento delicato caratterizzato da una contrazione delle attività e dei margini. In questo contesto il settore agricolo sta esplorando in modo...
-
Le tecnologie italiane per la transizione energetica ad All Energy Australia 2024
Si è chiuso, presso il Melbourne Convention and Exhibition Centre, All Energy Australia Exhibition & Conference 2024, il principale evento australiano dedicato al settore dell’energia con un particolare focus sulle energie rinnovabili. Partecipazione italiana grazie a ICE Agenzia...
-
Il primo parco solare di EDP in Spagna utilizza l’automazione di Comau
EDP, leader globale nel settore delle energie rinnovabili, testerà la tecnologia di automazione Hyperflex su larga scala per la costruzione del suo primo parco fotovoltaico in condizioni reali di installazione presso Peñaflor (Valladolid, Spagna). Il progetto, denominato...
-
Siemens insieme ad Alliander per accelerare la transizione energetica nei Paesi Bassi
Siemens e Alliander, una dei principali operatori di rete olandesi, con la sua filiale Liander, il più grande Distribution System Operator (DSO) dei Paesi Bassi, hanno avviato una partnership strategica per accelerare la transizione energetica e affrontare...
-
5 ragioni per investire in un futuro sostenibile
Investire su chi sviluppa soluzioni innovative per un futuro sostenibile non solo ‘va di moda’, ma è anche remunerativo per le aziende. Vediamo su quali ambiti conviene puntare La popolarità dell’investimento climatico è cresciuta esponenzialmente nell’ultimo decennio...
-
Solare a rischio di attacco, lo svela una ricerca di Bitdefender
Bitdefender ha pubblicato una ricerca sui punti deboli di una piattaforma di gestione di impianti fotovoltaici ampiamente utilizzata e di una piattaforma di inverter fotovoltaici. Le vulnerabilità, se accoppiate, potrebbero consentire a un hacker di ottenere pieno...
-
Agritech e digitalizzazione, l’IA di Vrai Lab per gli agricoltori non nativi digitali
Favorire la digitalizzazione per migliorare la sostenibilità economica e ambientale dei prodotti agricoli e assicurare le esigenze del consumatore in termini di sicurezza, tracciabilità e affidabilità. È questo l’obiettivo della partnership tra Vrai – Vision Robotics and...
-
Più sostenibilità con il monitoraggio dell’energia
I software di Schneider Electric permettono di analizzare e ridurre i consumi, migliorare l’efficienza e la continuità operativa di un processo altamente energivoro. I dati accurati raccolti con questi software aiutano Dife nella redazione del bilancio annuale...